Venla Elonsalo wins Näyttely24 award
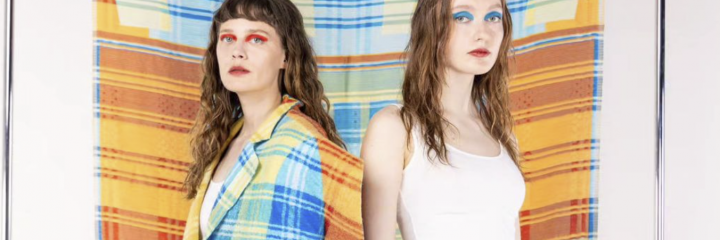
The awards from the graduation collections of MA and BA students from Aalto ARTS were presented on May 30th, 2024, as a part of the Näytös24 fashion show and Näyttely24 exhibition. You can see all the awards here.
Näyttely24 is a new event launched this year, and the award for it went to Venla Elonsalo for her MA thesis collection I Weave Clothes. The jury for the award consisted of Stephanie D’Heygere, Annabel Fernandes, Ane Lynge-Jorlén and Antti Kekki.
Read the description of Venla’s work below.
I Weave Clothes by Venla Elonsalo explores the design and production of multilayered woven garments and accessories that do not require any sewing. The collection is a woven collaboration with a Turkish weaving mill, Vanelli.
– Combining the expertise and facilities at Vanelli with my creative pattern cutting and textile design skills opens new realms to design possibilities in whole-garment weaving, Elonsalo says.
Cloth-weaving and garment construction are combined into one step. The fabric layers interweave together creating three- dimensional textile-forms. Both textile design and creative pattern cutting play an integral role in the design process. The weaving is done with industrial jacquard weaving machines. Therefore, the loom sets limitations for designs because the garments need to lay completely flat and fit into the weave repeat.
With her graduate project, Elonsalo challenges the conventional fashion system and supports woven textile-form design research. The combination of four-layered garment flattening, surface patterns, and fulling creates an artistic contribution. The work also provides utility beyond aesthetic novelty, by reviewing how digital tools have been implemented in the design process. These tools include clothing and textile simulation software CLO3D and Shima Seiki’s ApexFiz.
– I find it fascinating how complex three-dimensional forms can be created within weaving, a binary system, by either lifting or not lifting the warp yarns.
The main material used is wool. This enables fulled finishing, which is done after weaving and before cutting to prevent fraying of the cloth. Small details like metal fasteners help balance the softness of the fulled wool. Colors and the exaggerated seams communicate the four-layered woven garment construction visually. This offers an introspective view into the creation process by providing insight into the design process. Works by Maison Margiela, Issey Miyake and Rei Kawakubo have inspired Elonsalo’s concept creation.
– I experienced a sense of contentment when I figured out how the two-dimensional cloth could be converted into wearable three-dimensional form. My intention is to cultivate a similar sense of joy when my designs are experienced.
The use of industrial weaving machines supports made-to-order production. Making garments on-demand is usually difficult to achieve at a price point that is comparable with conventionally produced products. However, when production is developed toward automation, it is more profitable to construct garments in high wage economies.
Even though post-weaving cutting is required, there is a significant reduction in manual construction steps compared to the industry standard cut-and-sew production. Currently, it is possible to knit whole garments industrially. However, for weaving, the development is still in the beginning. That is why I Weave Clothes thrives to find solutions that inspire the development of multi-layered woven garments that will revolutionize the fashion making process of today.
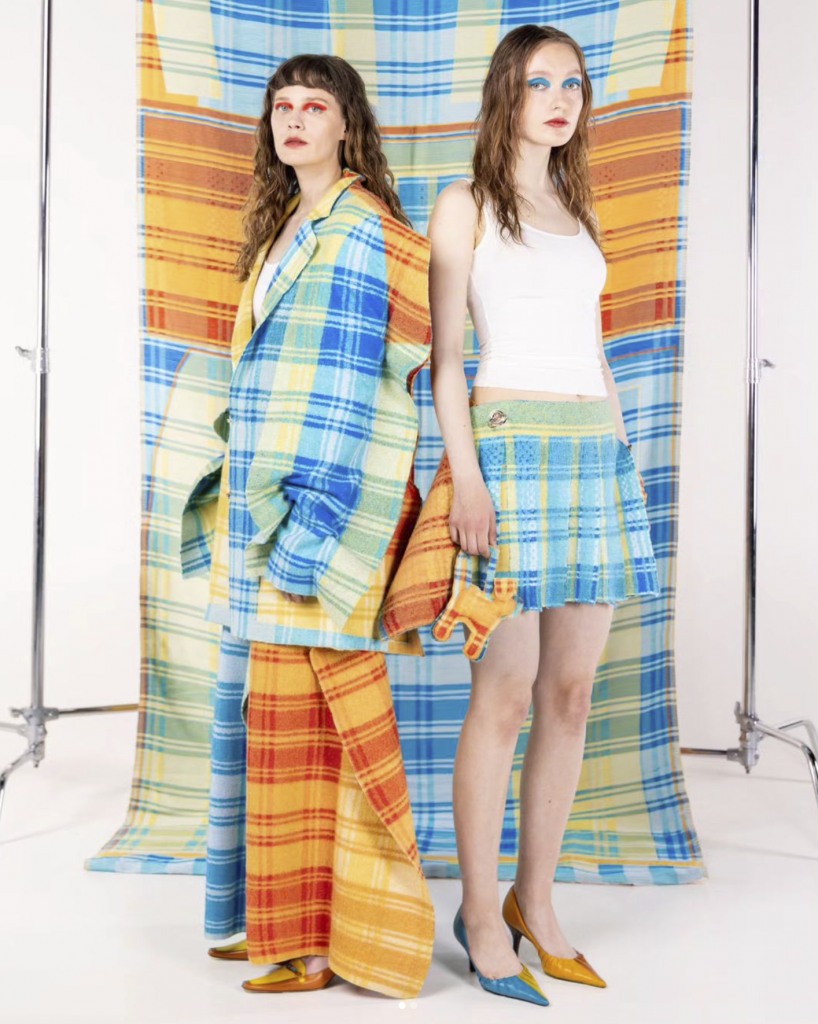